CASS / ASS Test
CASS / AASS, SSe / SS Series Salt Spray Corrosion Test Chambers, also known as Saline Cuproacetic Mist Chamber, have been built to meet the requirements of ASTM B368, ASTM B117, ISO 9227 CASS / AASS – JIS Z 2374 CASS / AASS.
The following are construction characteristics of the equipment that are very important to ensure the repeatability and reproducibility of each test. These tests are comparative, so they must follow the exact construction methods of the standards.
– Indirect uniform heating through a water jacket on all sides of the equipment (page 8 of ASTM B117, ASTM B368).
– A lid with a smooth inner finish and a 100 degree angle to avoid dripping on the samples (pages 1 and 8 of ASTM B 117).
– SD Card, saves real-time test parameters, just open Microsoft Excel to display the chart of every cycle.
– Construction according to UL508.
– All components used are UL listed.
– 600 – 1300 – 3,000 – 5,000 (other dimensions available upon request)
– Equipment is constructed with inert materials that do not interfere in the final result of the test.
– Full color Touch Screen.
SSe Series:
Allows you to program mode (Salt Fog) CASS / AASS;
SS Series:
Allows you to program fully automatic cycles with different modes:
– Salt Spray mode (Salt Fog) CASS / AASS
– Condensed Humidity Mode
– Natural Dry Mode
– Soak Mode
– SWAAT TEST mode – ASTM G85 Ap.3
Application:
These chambers are used to conduct rapid tests on copper / nickel / chromium or nickel / chromium / coated steel parts / glass / mirrors / plastics, iron and zinc chrome coatings for relatively severe use, and aluminum, especially when anodized .
Its application primarily serves companies in automotive, civil construction, plastic, aviation, oil and gas, paints, varnishes, electronics, chemical, metallurgical and other industrial sectors.
Operation:
The test samples are arranged inside the test cabinet according to technical norms or custom company standards. They are exposed to a controlled high humidity mist solution with pH 3.0, acetic saline with addition of copper dihydrate at a temperature of 50 degrees Celsius, for certain time periods as specified by industry standards or company standards.
After this exposure time period the samples will be evaluated according to the technical standards that determine the degree of oxidation and / or type of corrosivity, as well as any further evaluations.
Main test standards:
ASTM B 368 – ISO 9227 – JIZ J 2374 – MILs – IEC – DIN – SAE – and etc …
Corporate rules VW-FORD-GM- RENAULT-NISSAN – HONDA – YAMAHA – Mercedes Benz Scania – Citroen – AUDI – BMW – other consult us.
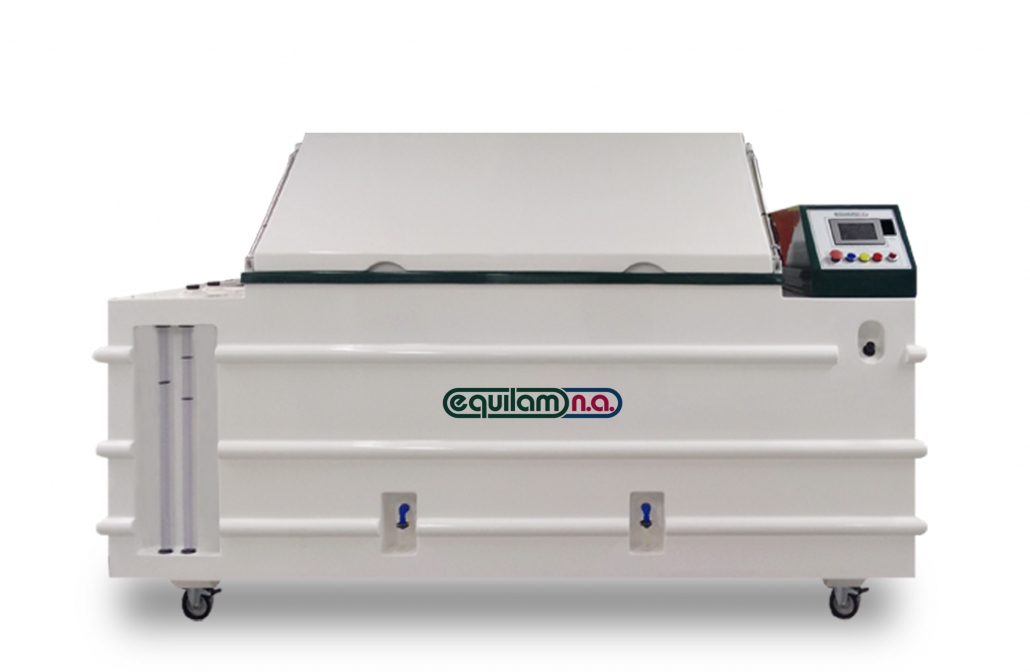
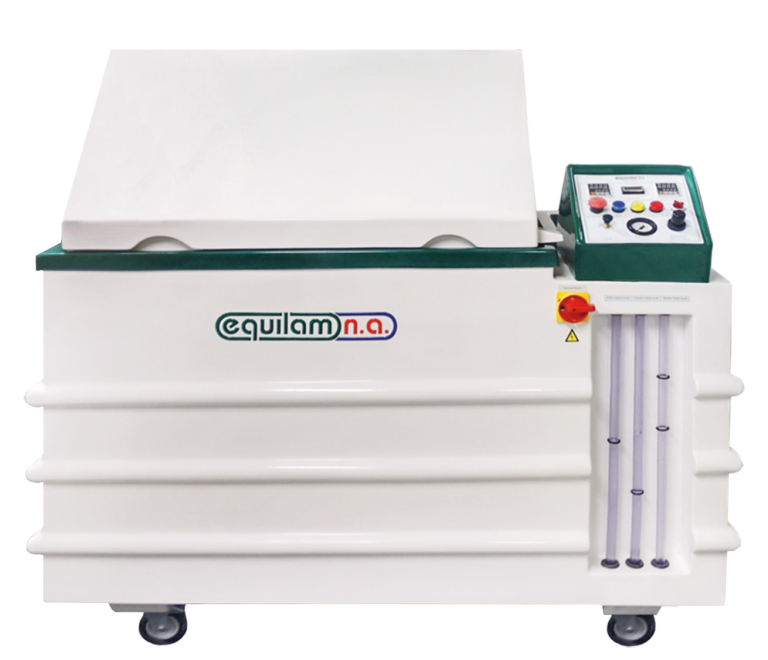
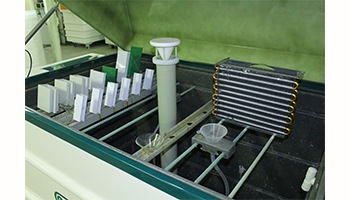